How is your safety process working? Is it providing the results you want?
We provided information on how to develop a safety program in our fall webinar. Now, let’s evaluate the process. Is your loss experience based on a solid safety process, or is it luck? Long term safety success is based on fundamental elements and execution. This execution can be difficult at times. You can determine if your process is based on solid fundamentals by conducting a Safety Management System (SMS) evaluation.
Conducting a SMS evaluation is not as simple as checking the box indicating your operation has a particular process in in place, but rather an in-depth evaluation of the safety process you have in place and whether or not the elements are providing the desired outcomes. You may have a program to lockout equipment and have not had any losses, but can you say that 100% of the time your employees are following the process, or that the process is 100% compliant? If you cannot answer the above question with 100% confidence, you are a candidate for a SMS evaluation.
Most processes can have anywhere from 15-30 main elements and then sub-elements within the main elements. Elements are both best practice and regulatory in nature. All regulatory elements must be in place, while the best practices will provide a path to world-class safety and health.
Some of those elements on the regulatory side consist of, but are not limited to the following:
- Control of Hazardous Energy
- Fall Protection
- Hazard Communication
- Confined Space Entry
- Powered Industrial Trucks
- Emergency Action Plans
- Electrical Safety
- Personal Protective Equipment
- Scaffolding
- Bloodborne Pathogens
- Silica
- Hearing Conservation
- Machine Guarding
- Respiratory Protection
Additionally, a world-class process will also include best practice elements which would consist of the following, and a few additional elements based on your exposures and needs:
- Management Leadership and Planning
- Accountability
- Safety Inspections
- Fleet Safety
- Contractor Health and Safety
- Employee Involvement
- Job Safety Analysis
- Health and Safety Training
- Industrial Hygiene
- Medical Services
- Note: Some best practices also have a regulatory component.
So, you have these elements and you want to know if they work. You will need to evaluate what exists. This can be done through evaluating the current programs, interviewing managers, supervisors, and workers, and making observations. Some evaluations stop at the Paperwork evaluation, but a thorough SMS evaluation will include a review of documentation, interviews, observations, and follow up interviews. For a facility with 100-150 employees this could take up to 3 days. While this may sound like an OSHA inspection, it goes beyond OSHA and evaluates not only what needs to be done from a regulatory practice, but what is done to assure the processes are working at the levels you expect. We look at basic levels (OSHA for regulatory elements) system levels (internal requirements) and advanced levels to achieve “World-Class”.
Finally, we add Point values to the audit elements to provide an effectiveness score. Scoring can vary as long as there is an agreed definition for the assigned value. An example may include a 1-10 point system for each element, or a 0-2 point value for each element. (Join us for our March 15th webinar for more details on the point values). It is most important to agree on a system and stick to it for consistent evaluations.
The Bottom Line: If you are not evaluating what you are doing to determine if the systems are working, you may leave your company exposed to a major loss. This could be either a financial loss, human loss, company reputation, or a combination of those. Safety Management System evaluations will give a scorecard and help you determine the processes that are working the best, and where organizational safety needs to be focused for the best results.
Register for Rick's Webinar, Evaluating the Effectiveness of Your Safety Process, to learn more about how to take your Safety Program to the next level.
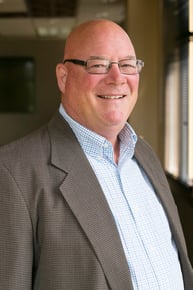
COMMENTS